How digitalization can help the hydrocarbon sector boost efficiency and cut emissions
19 April 2024
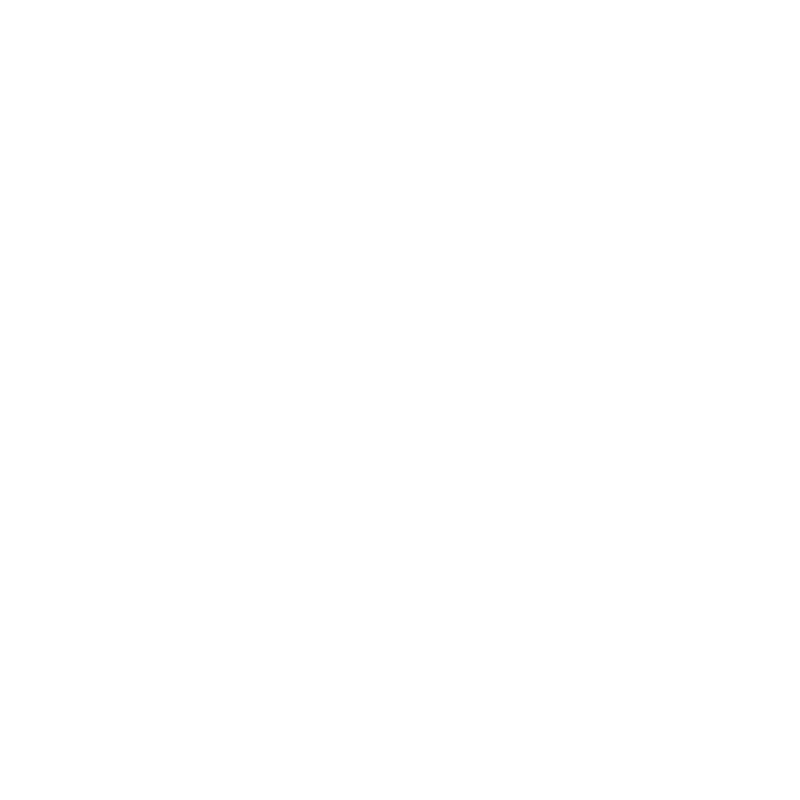
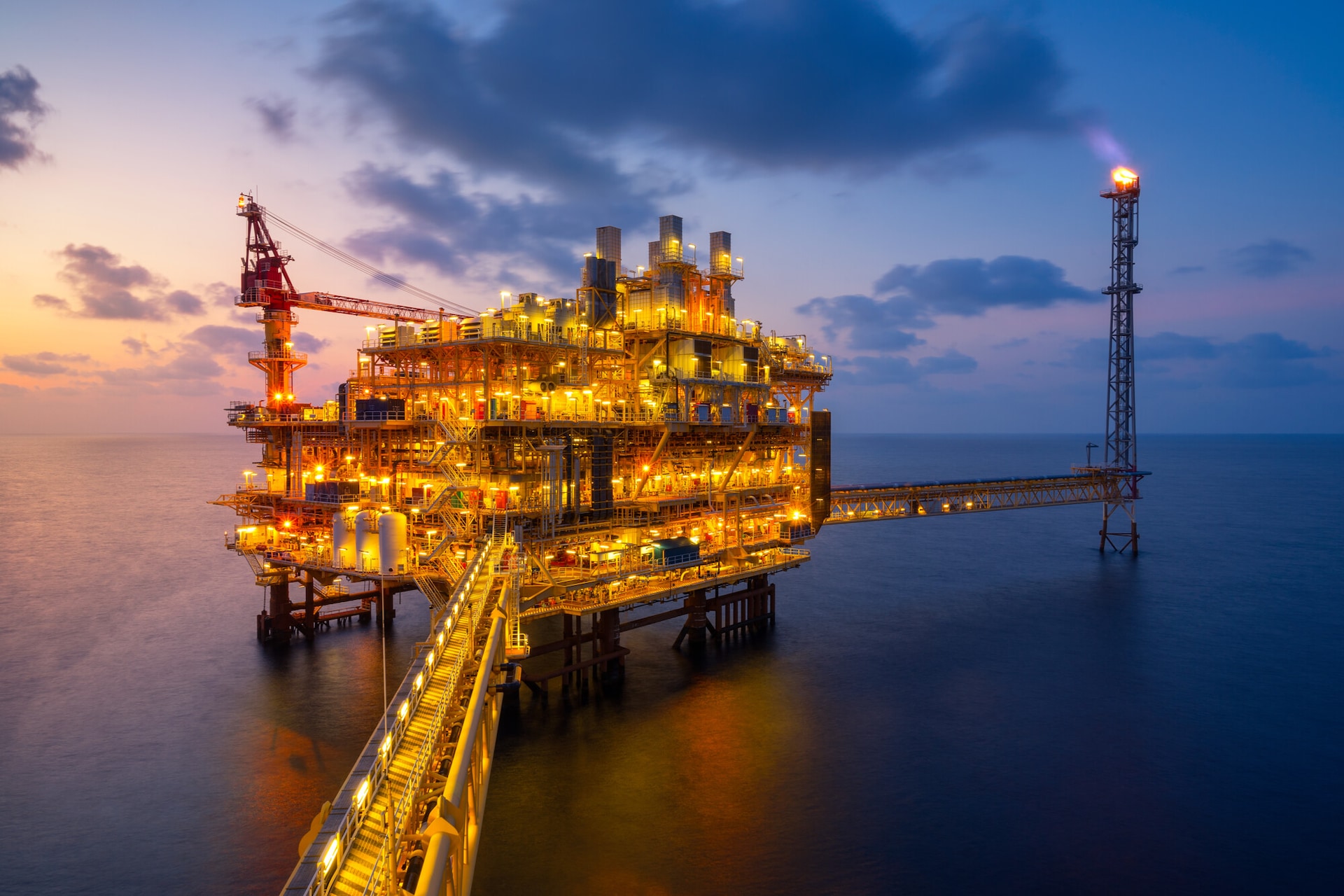
As the world grapples with the huge challenges posed by climate change, the global demand for oil and gas remains high despite mounting calls to reduce the reliance on fossil fuels. A fact underlined by the International Energy Agency (IEA) when it warned that surging consumption levels could make it increasingly difficult to even adhere to the Paris Agreement goal of restricting the rise in average global temperatures to 1.5 °C.
Fortunately, the transition to renewables is gathering pace but energy producers must do their bit to operate in a more efficient and sustainable way in the interim period.
Digitalization transforming energy production
The hydrocarbon sector can immensely gain from Industry 4.0. By modernizing and optimizing their diverse architecture and using a combination of hardware, software, and connectivity solutions it can reap the full benefits of digitalization that could not only boost productivity but curtail carbon emissions as well. The industry is taking steps to go digital, however Nokia and ABI Research’s Industry 4.0 Maturity Index indicates further scope for improvement. The survey which involved 500 companies in five key markets shows that oil and gas companies are trailing behind peers such as fabricated metals and electronics and appliances in their digital journey.
The difficulties faced by fossil fuel producers are unique. Integrating modern technologies with existing infrastructure is not easy. The good news is that a comprehensive set of innovative solutions like artificial intelligence (AI), augmented reality (AR), and big data are available to help industries build digital capabilities at a large scale.
Bringing to bear the full potential of Industry 4.0
From instant tracking, automation and process improvement to preventive maintenance and collaborative group chats, Industry 4.0 offers a variety of solutions.
These next-generation technologies can totally revamp operations by giving personnel, more power to monitor and handle assets, strengthening safety and compliance standards and by creating value from a wealth of accessible data.
By using new applications and devices with widespread, dependable wireless connectivity and edge computing, Industry 4.0 enables people, processes, sensors and legacy machines to function as a unit.
For instance, oil and gas extraction (offshore and onshore), transportation via miles of pipelines, storage facilities and processing at refineries for final distribution, is a huge end to end task. The working conditions are fraught with risks, and not to mention the supply chain which fluctuates frequently.
This is where digitalization comes into play. By using tools like Internet of Things (IoT) devices, automated robotics, and digital twins, oil and gas producers can connect their IT (Information Technology) and OT (Operational Technology) environments, resulting in a complete transformation of their business processes.
As a way of expanding the existing instrumentation in the oil and gas industry, IoT devices are being installed at industrial sites. A secure and dependable method of connecting and gathering data for a completely automated site is to merge all industrial protocols into one platform that sends the information back to the relevant systems for local and remote analytics.
One crucial advantage of such a process is superior situational analysis. By using IoT sensors, wearables, and bodycam footage with real-time analytics, one can track the precise location, exposure, and movement of employees and assets as well as watch vital health statistics – helping to protect staff from danger. This can result in better decision-making, enhanced readiness, and quicker response times.
Additionally, Unmanned Aerial Vehicles (UAVs) can improve intelligence and safety. Using drones with thermal cameras for inspecting oil rigs structures, pipelines and plants can reduce the risk for workers. Connecting these drones to a flare stack can help to measure excess hydrocarbon gases, assisting in efforts to keep within emission limits and locating a leak in a pipeline.
Staff can use more tools to stay safe while working. For instance, robots can check how risky an area is. They have sensors that can sense and measure different elements including gas, water, and other dangers or reach pipes in hard-to-get places during corrosion inspections.
Entering the world of industrial metaverse
Augmented reality and the "industrial metaverse" are gradually making their way into the energy domain, too. The industrial metaverse allows humans and digital solutions to interact by fusing the physical and digital worlds. This has a direct impact on how we manage and monitor physical assets and operations.
Digital twins are one of the first uses of the industrial metaverse. A digital twin is a replica of a network or asset that lets operators track how well they work and visualize the whole system. This can help them avoid bottlenecks, find weak spots, and decide where to assign more resources.
Digital twins can also be used to test scenarios and help teams prepare in advance before applying them in the real world. For example, it can track network performance as well as mobile devices and IoT sensors to find and reduce or anticipate errors at the network or device level. At the same time, crisis planning for cyberattacks, natural disasters or other risks is now possible – realistically simulating worst case scenarios so staff are better prepared.
Charting a course to digitalization
To enable digitalization and intelligent applications, reliable private networks are essential. The enhanced connectivity offered by LTE/5G private wireless has become key to that end. With built-in reliability, quality of service, and security, private wireless networks can deliver the necessary prioritization per application, a multiservice approach, and real-time data collection for robust automation capabilities and reliable predictive analysis.
IoT sensors and ruggedized smart devices and applications for remote and automated operations can make oil and gas operators even more data driven. This is a welcome development. Even in locations that are far away or dangerous, they can generate more data about their operations and the environment.
An intuitive communications infrastructure that can perceive, reason, and act, and help the industry to develop the resilience and digital skills it needs is essential.
Read more
About Nokia
At Nokia, we create technology that helps the world act together.
As a B2B technology innovation leader, we are pioneering networks that sense, think, and act by leveraging our work across mobile, fixed and cloud networks. In addition, we create value with intellectual property and long-term research, led by the award-winning Nokia Bell Labs.
Service providers, enterprises and partners worldwide trust Nokia to deliver secure, reliable and sustainable networks today – and work with us to create the digital services and applications of the future.
Media inquiries
Nokia Communications, Corporate
Email: Press.Services@nokia.com
Follow us on social media
LinkedInTwitterInstagramFacebookYouTube