Accelerating decarbonization: The digital revolution in industry
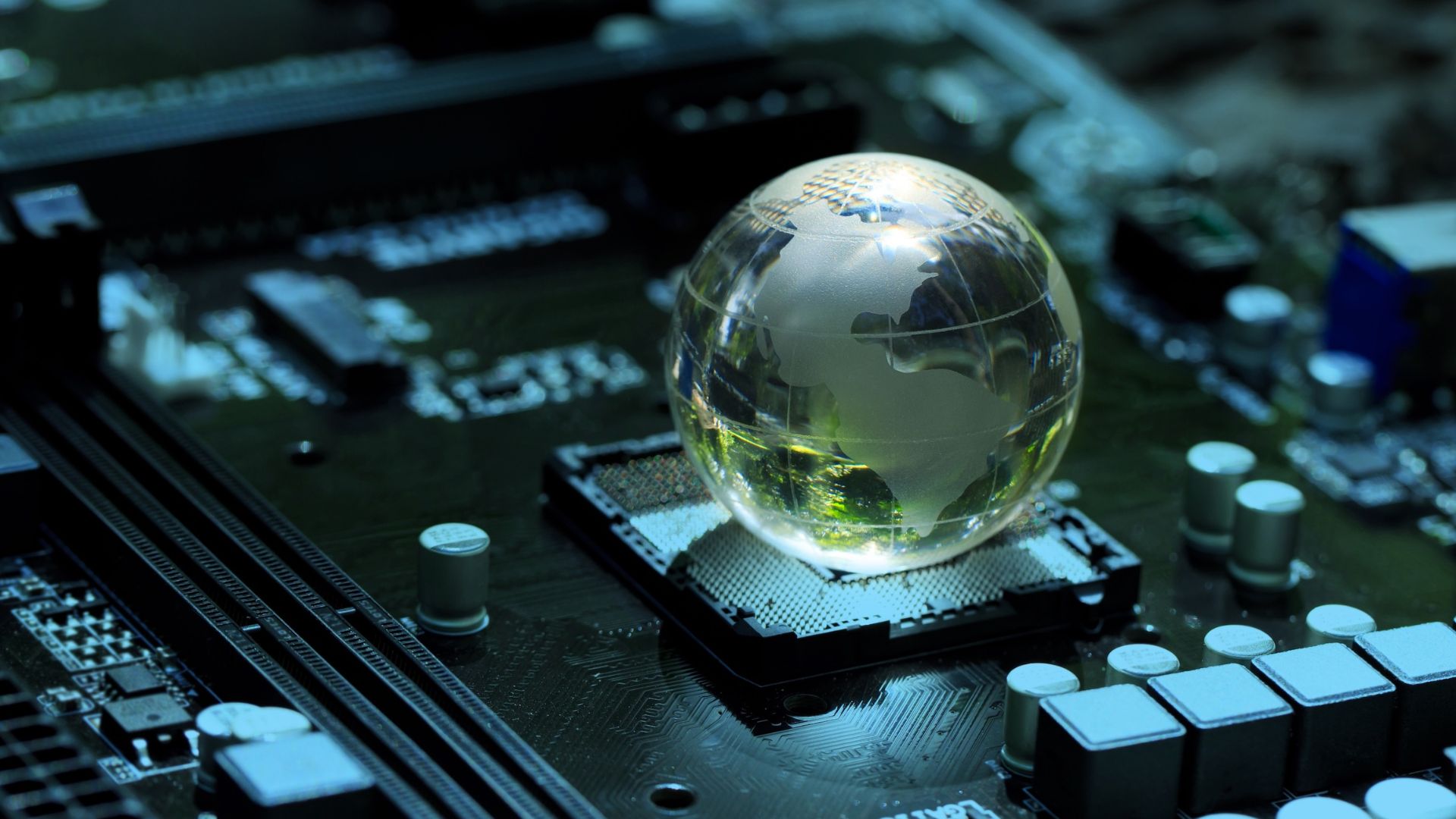
Reducing emissions to achieve net zero is a top priority for many industries. However, enterprises operate in highly competitive markets, so decision-makers must simultaneously increase business performance. Digitalization is the key to unlocking industrial sustainability and operational and financial benefits, helping enterprises to achieve their goals.
Efficiency = profitability and sustainability
Studies have already shown how digitalization drives new efficiencies, impacting the bottom line as well as sustainability. A study found that 79% of enterprises reduced emissions by at least 10% using digitalization technologies, while recording similar or higher productivity, efficiency and worker safety gains. 78% reported a positive ROI within just 6 months (GlobalData and Nokia, 2024 Industrial Digitalization Report).
Digitalization offers myriad opportunities to make industrial operations more efficient, profitable and sustainable, from video analytics and environmental sensing to remote machine control and energy monitoring. For example, implementing remote monitoring and wireless video analytics on a manufacturing production line improves quality inspections and can lead to 30% fewer defects, reducing rework, material waste and associated costs (Nokia Bell Labs). One of our discrete manufacturing customers increased efficiency by 25% while lowering energy consumption when they moved AGV operations from Wi-Fi to more reliable private wireless connectivity. Another saw the average distance traveled by a robot decrease by 28%, increasing efficiency of the robot while lowering energy consumption.
Read on to discover key digitalization use cases and technologies that could help you achieve your sustainability, efficiency and profitability goals.
Critical worker communication
Equipping workers with ruggedized devices and critical communications applications, such as push-to-X, to talk and share data and video with one person or many, is a great starting point. This reduces worker movement and the potential for incidents when dozens, if not hundreds of workers must traverse hazardous areas alongside manned, remote-controlled and autonomous machines and vehicles. With more information shared, operational problems can often be solved by on-site teams or experts working remotely, avoiding unnecessary truck rolls to reduce emissions and more rapidly resolving issues that can see energy consumption spiking.
Drone inspections
Drones are the biggest driver for emissions reduction on industrial sites (GlobalData and Nokia, 2024). Industries can reduce truck rolls, fuel and worker safety risks by deploying drones for perimeter surveillance, hazardous area monitoring and remote inspections of high structures and other difficult-to-reach infrastructure assets at mines, ports, oil and gas plants, offshore facilities and other sites. They can be dispatched faster with minimal or no impact on operations, for example, to rapidly show the effect of blasting at mines. Teams can detect issues and find resolutions faster, reducing downtime and the impact on worker safety and the environment.
Digital Twins and predictive maintenance
According to GlobalData, IIoT sensors and digital twins are the second biggest drivers for reduced emissions on industrial sites. Using real-time data from connected sensors and devices, enterprises can continuously monitor critical equipment and detect anomalies before failure occurs. For instance, when a motor malfunctions, through wear and tear or overheating, it often consumes more energy. Predictive maintenance enables enterprises to intervene early, avoiding costly breakdowns and unplanned downtime, reducing fuel spikes, and extending equipment lifetime.
At one Finnish port, real-time digital twin and video-based situational awareness are cutting emissions and boosting efficiency and worker safety. Inbound vessels are given their expected berth location in advance, allowing them to adjust speeds and reduce offshore waiting times, resulting in fuel savings of up to 3,000 Euros per vessel, per port call.
Remote control and autonomous vehicles
By automating haulage trucks at mines, worker safety, process accuracy and overall efficiency increase. Through dynamic routing and optimized vehicle control, including braking and acceleration, trucks operate more efficiently and consume less fuel. Our mining customers can see fuel consumption reductions of 7% and efficiency increases of 8.5% using autonomous trucks. Mechanical wear and tear is also reduced and truck lifecycles are extended.
These improvements have been achieved by implementing robust, reliable private wireless networks. Before this, using Wi-Fi alone, handover delays between access points as trucks traversed the site meant they could slow or halt, requiring a manual restart that impacted productivity and potentially worker safety.
At ports, under pressure to reduce emissions while handling a growing volume of containers, sustainability efforts must be tied into improving container handling efficiency. By connecting and automating cranes and straddle carriers, schedule changes are accommodated rapidly to improve vessel turnaround times, reduce emissions and enhance safety. Our research shows that operating quay and stacking cranes enables reliable remote control and can improve container handling efficiency by 10%, meaning productivity is maintained at lower energy consumption. Similar to our mining example above, this is achieved through high network reliability using business-critical private wireless and industrial edge compared to Wi-Fi only.
A robust technology foundation for sustainable change
Whatever digital solutions you use to achieve sustainability goals, you need a robust, flexible and scalable digitalization foundation. Our edge compute and AI platform for industries incorporates business-critical 4.9G/5G private wireless, and access to DAC Marketplace from which you can deploy Nokia and trusted third-party industrial applications and devices. The platform easily integrates with existing technology environments, provides real-time data processing capabilities, and serves as a single hub for all your operational data, empowering you to launch any number of digitalization and real-world AI use cases that support your sustainability and wider operational goals.
Use the Nokia Private Wireless Sustainability Calculator to estimate how these technologies can help you reduce your environmental footprint, or download our sustainability guides for chemical manufacturing and port terminals to learn more about digitalization use cases and the components required for successful implementation.