Industry 4.0 innovation thrives on collaboration: Advancing the 5G smart factory at ARENA2036
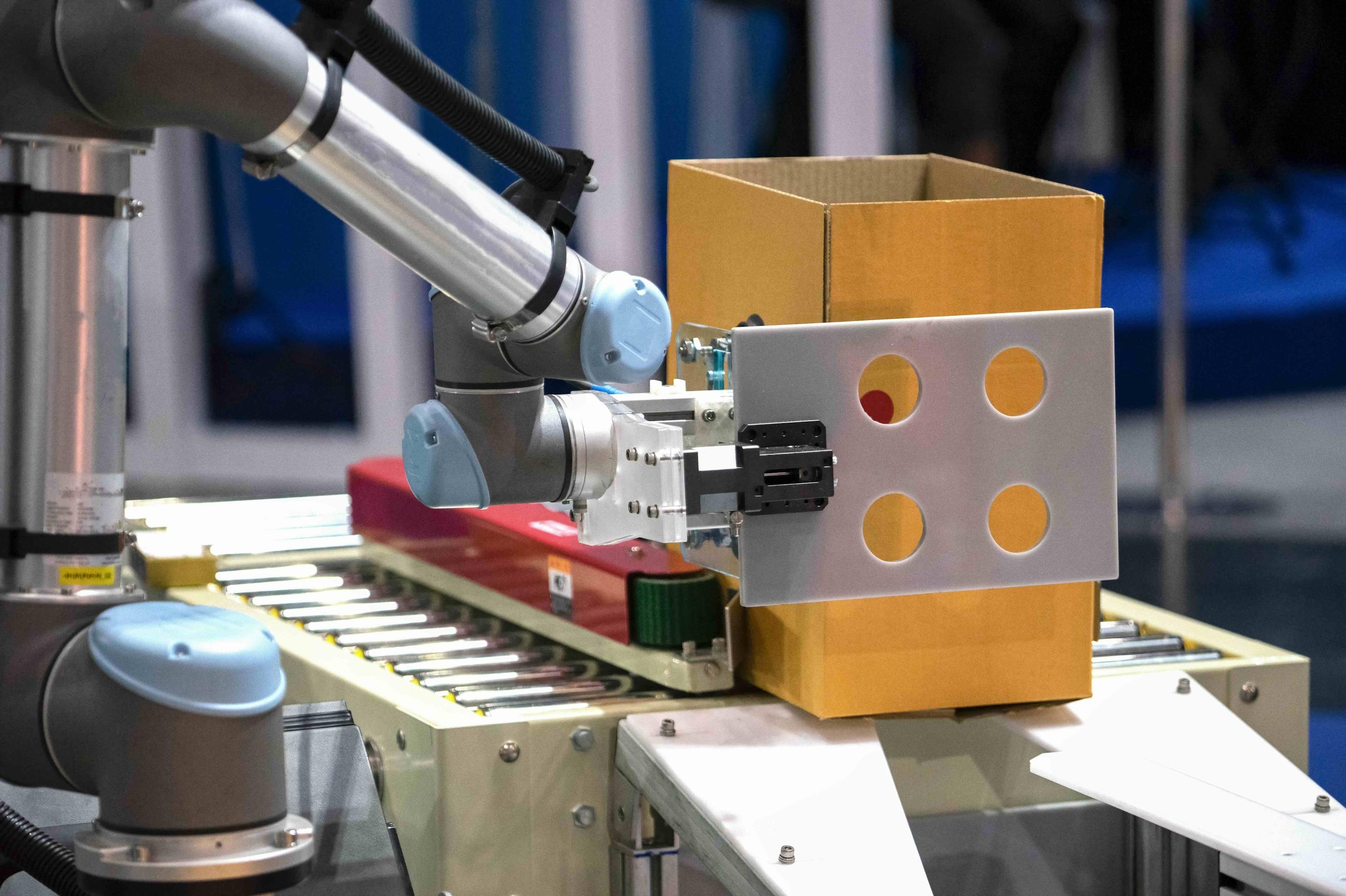
At ARENA2036 in Stuttgart, Germany, Nokia and more than 20 partners made history with the world’s first demonstration of parallel 5G manufacturing automation use cases — proving the vision of the smart factory of the future and the power of a cross-industry innovation ecosystem.
5G is the first mobile network release designed specifically with industry needs in mind. Its ultra-low latency, consistent availability and high data-transmission rates make possible a whole range of industrial use cases that were simply out of reach with earlier technologies. As more 5G spectrum becomes available, manufacturers — especially those in the automotive industry — can start building their own private wireless networks and 5G smart factories. These can help them take automation and digitalization to the next level, bringing substantial improvements and innovations into the way cars, larger vehicles and many other products are built.
Ecosystem partnerships and cross-segment collaborations like ARENA2036 enrich and accelerate the innovation process: manufacturers bring their deep knowledge of processes and the results they’re after; technology companies can then propose solutions that offer new ways of achieving them. In our case at Nokia, it’s about proving how 5G networks can help our customers deliver on their business goals. Bringing different perspectives together makes it possible to identify and develop innovative solutions that might not have been obvious in isolation. That focus on coming together to explore new ideas was at the heart of the ARENA2036 concept.
5G manufacturing partnership in action
The ARENA2036 event, held virtually in November 2020, showcased two key 5G smart factory use cases, developed in collaboration with automotive industry giants Daimler and Bosch. The first case focused on automated guided vehicles (AGVs), which play a critical role in making manufacturing facilities more efficient. AGVs can move parts and components between warehouses or across the shop floor and perform other routine tasks so human workers can contribute their skills where they add the most value.
Traditionally, the movement of AGVs has been limited to strictly defined paths controlled by magnetic tape or other similar mechanisms. In those situations, if something falls onto the path and blocks the AGVs, the vehicles have no way to move around it and their productivity stalls.
In our November demo, we showed how AGVs equipped with LIDAR (light detection and ranging), video and other sensors and supported by 5G connectivity can be given the situational awareness to move freely throughout a factory. These 5G-powered AGVs can identify and go around stationary obstacles — and avoid collisions with moving hazards and people. With fleet management control, these AGVs can share situational information, so if a particular aisle is blocked off, for example, all AGVs know to take a different route.
5G’s ultra-fast responsiveness makes it easier and safer for AGVs and other machines (such as robots and co-bots) to work with each other and with humans. Sensors on AGVs and 5G-enabled devices ensure they don’t interfere with the actions of those around them and, in case of an emergency, wireless full shutoff is effectively instant. The demonstration of 5G for this critical manufacturing industry case was such a resounding success that both Daimler and Bosch now plan to deploy this technology in their plants, improving efficiency and safety for their operations.
The second use case at the ARENA2036 event was a collaborative project called FlexCAR — an open platform with hardware and software interfaces that enables rapid product development and innovation across the ecosystem of original equipment manufacturers, suppliers and application developers. For example, as vehicle systems become increasingly digitalized, they require specific versions of software. With reliable 5G connectivity throughout the shop floor, the customized vehicle software can be downloaded automatically at exactly the right moment during assembly. This means the software is always up to date with the very latest version at the time of installation. Where customer information is available, FlexCAR could even pre-load customer-specific data to produce a more personalized product right off the assembly line.
ARENA2036: An innovative approach to development and testing
The facility hosting the virtual demo, ARENA2036, arose out of the Industrial Communications for Factories (IC4F) consortium. IC4F was launched in 2017 to develop and demonstrate secure, robust, real-time communications solutions that will improve automation and digitalization in manufacturing, supply chain and logistics. You can read more about our work on the IC4F project in my colleague Markus Fessler’s blog, “How a near-miss forklift accident is helping architect the future of industrial communications.”
While IC4F is now winding down, the ARENA2036 project is just getting started. The concept itself is innovative, hosting multiple industry partners to develop and test manufacturing automation use cases holistically in a “real-world” setting. This is different from traditional approaches that develop use cases in isolation — without understanding how they might work together or how a single network might prioritize multiple competing use cases. Testing innovations in an environment like ARENA2036 gives a better picture of true feasibility and makes it easier and less risky to deploy solutions in working factories and other settings.
The AGVs and FlexCAR use cases were developed primarily by and for the automotive manufacturing industry, but both have cross-industry applicability. Automatic software installation and configuration can be applied in a variety of manufacturing settings, allowing the “smart screwdrivers” used on assembly lines to be reprogrammed instantly for different vehicle models or other products. Situationally-aware AGVs can be used in warehouses, port terminals, smart cities or airports — some of which have even more complex navigational environments than smart factories — and the same principles can even be applied to drone management.
Stay tuned for more 5G-enabled manufacturing enhancements
Throughout the ARENA2036 project, I’ve been consistently impressed by how well all the partners, including direct competitors, have worked together. By being open to learning about and from each other, we’ve worked to develop some really outstanding initiatives with far-reaching implications for the automotive industry and beyond. We’ve come a long way on Industry 4.0 in the past year, and I can’t wait to share even more exciting advances with you as we move forward.
If you want to learn more about Nokia’s Industry 4.0 vision and solutions or 5G ACIA join me and a number of leading Industry partners at our 5G Smart Manufacturing Summit. Watch now and join in the conversation.
Click here to learn more about Nokia solutions for manufacturing, supply chain and logistics.