The hidden costs and inefficiencies of poor situational awareness in industrial operations
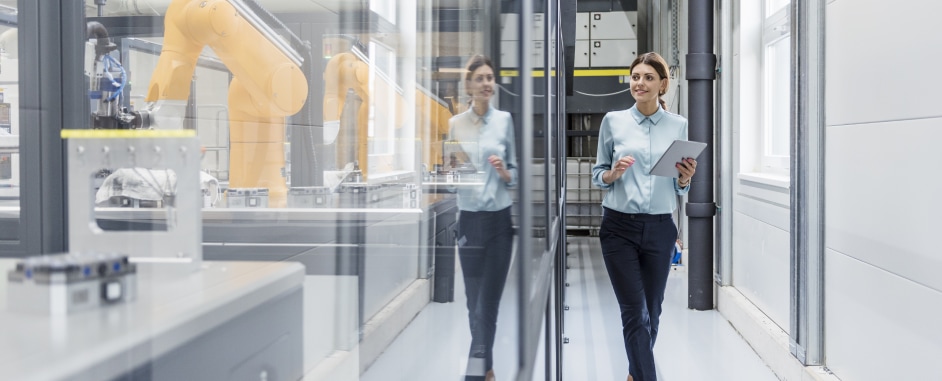
Anyone managing or working in an asset-intensive industry will understand the challenges associated with tracking tools, materials, vehicles and even workers to ensure the efficient flow of operations. But do you know the real costs associated with not doing that effectively and the impact that can have on your business? One study found inefficient resource utilization contributes to €630 billion in costs for European industries! 1
The hidden inefficiencies within your operation
Thinking about your own business practices, can you identify inefficiencies around asset utilization? If you can’t, you aren’t alone, and if you think you can, you’re probably underestimating the full extent of the problem, as they are often hidden. Maybe you think your fleet of forklifts, AMRs or other industrial vehicles are being properly utilized, but what if you’re using the same vehicles time and again, with others frequently left idling out of sight? If maintenance costs are rising, that could be an indication that you need to track and balance usage.
Another common issue is equipment going missing: 20% of workers’ time is spent looking for their tools.2 A glance through procurement systems may give you an idea of replacement costs but won’t inform you about the downtime and productivity losses incurred. And it’s not just tools that are often misplaced: goods, materials and specialist equipment all too easily become scattered across large industrial sites and impact operational efficiency.
Stock control, customer relationships and worker safety can be impacted too. A study of manufacturers found that the average firm was holding $142,000 of stock 3 over and above what was required for the year. And, as asset-intensive industries like manufacturing and port terminals accelerate their digital transformation, gaining awareness of the movement of heavy machinery and autonomous vehicles will increasingly become a priority to ensure worker safety and protect expensive equipment.
It’s clear that if companies lack the ability to properly track assets, they’ll end up paying through time, workers and capital!
Elevate situational awareness and address inefficiencies
One of the many compelling use cases enabled by Industry 4.0 is real-time tracking and positioning and its introduction will bring new levels of awareness around inefficiencies, allowing enterprises to make better-informed decisions to optimize business processes, costs and productivity.
By tracking your physical assets, you’ll gain more than just awareness of where your assets are at any time – you’ll also be able to understand how they are being used, the frequency of use and how they are moving around your site. Equipped with this information you can identify bottlenecks and efficiency drains and implement measures that allow you to improve productivity, making you more competitive.
You will, for example, be able to analyze vehicle usage and balance it across your fleet to avoid bloated maintenance costs and improve asset ROI. You can reduce delays and downtime by ensuring vehicles, machines and other specialist equipment are stored in their assigned locations and that workers can locate tools and materials instantly. You can see if vehicles and goods move smoothly throughout your site and detect inefficient layouts or other workflow hindrances that cause bottlenecks. And you can save precious time when locating workers during an emergency.
Choose the right asset tracking capabilities
In many industrial sites, tracking and positioning is often a primary reason for improved resource utilization and reduced downtime at the facility, because enterprises have greatly extended visibility into the whereabouts of their various assets.
So, how do you improve tracking and positioning for your business? Depending on your industrial environment and use case requirements, a variety of solutions with different underlying technology capabilities are available to address your needs. For example, if you want to track assets that are predominantly used outside, then a solution specifically designed for high-precision outdoor tracking may be what you need. If you don’t want to equip assets with physical tags, you can use intelligent camera-based positioning to quickly locate vehicles and specialist equipment, or workers in distress. Using real-time video feeds from your on-site camera systems this way can add an entirely new level of situational awareness to your operation. And by coupling it with far-edge compute and AI capabilities, you can make faster, better decisions and benefit from advanced automation.
Whatever your requirements, you must implement robust connectivity and on-premises edge computing capabilities to ensure reliable and secure real-time processing of often sensitive and mission-critical OT data. With this in place, you can build a robust foundation for real-time tracking and positioning to drive productivity and efficiency, benefit from more sustainable, lean operations and reduce your costs.
How much asset visibility do you have?
If I were to ask again how poor situational awareness could be impacting your business, could you now think of inefficiencies that could be addressed through real-time tracking and positioning? Without it you are paying the price of lack of visibility every day, and that will adversely impact productivity, your people and your profits.
Through real-time tracking and positioning you will be able to bring those inefficiencies into the light and use insights generated deep within your operations to address them and create significant business value.
Interested in learning more? Download our digitalization guide ‘Revolutionize operational visibility in manufacturing with real-time tracking and positioning’ to understand how you can transform your operations.
Sources
-
Greenovate Europe
-
Sandvik Coromant
-
Unleashed Software