What ‘the network’ means
in Industry 4.0
How use cases define Industry 4.0 network architectures
222 hours. That’s how long it would take to transmit two gigabytes over the RS-232 standard, introduced in 1960 and one of the first standards to allow point-to-point communications between two devices. Times have changed. Today, millions of devices are talking to each other at the same time, transmitting terabytes of data — enabling everything from autonomous robots on factory floors to artificial intelligence that identifies and addresses manufacturing bottlenecks in real time. With Industry 4.0, the way we communicate is changing. But we also need to change the way we think about the underlying networks.
Rethinking the network is critical because it is the fundamental enabler of the type of interconnectivity that defines Industry 4.0. But what kinds of networks are we talking about? And what do they need to do differently than the networks that have come before? Knowing the answers can give companies an undisputed competitive edge.
Getting those answers isn’t easy, however, because there’s no hard line separating Industry 3.9 from Industry 4.0. A lot of it looks the same. But there is a threshold of complexity that, once crossed, requires a radical leap forward in intelligent connectivity. Most companies have already crossed it, finding themselves immersed in a new world of almost infinite information. Data is being continuously generated in new places and used in new ways by increasingly interconnected systems, driven by analytics and automation in what are known as “cyber-physical” systems.
All this information requires a powerful, resilient and intelligent network.
“The network is one of the building blocks, the primary components,” says Jefferson Wang, Senior Managing Director and Global 5G and Networks Lead at Accenture. “You need real-time data, devices, sensors… and something needs to connect all of it together.”
What kind of network is needed for Industry 4.0?
The networks that have supported and connected digital communications over the past decade weren’t built to make the most of Industry 4.0’s potential. So what does an Industry 4.0 network look like? There is no one answer. It all depends on the use case: what’s needed for augmented reality applications, for example, isn’t the same as what’s needed for advanced robotics. Any given use case may involve a whole mix of technologies, including 5G, private LTE, artificial intelligence, machine learning and the Internet of Things. But most importantly, these networks need to be purpose-built.
“The networks in industry today are often special-purpose, disconnected from other networks, and operated in silos. They weren’t engineered by network architects,” explains Ben Brillat, Global Domain Leader for Next-Gen Wireless/5G and Edge Communicating at Kyndryl. “Industry 4.0 networks have significantly increased requirements for connectivity - they need to be engineered as part of a total enterprise environment to deliver reliable and secure communications, by people expert in network systems.”
Industry 4.0 needs specially designed networks not just because of the technologies involved, but also the variability of requirements from the host of possible use cases. Networks can be built to prioritize resilience, uptime, response time, latency or any number and combination of characteristics — all of which may change over time as Industry 4.0 use cases grow and evolve.
“The biggest mistake is thinking the network is static,” says Wang.
While it’s clear there is no one-size-fits all set of requirements for Industry 4.0 networks, real-time data collection and processing are essential to unlocking many of the potential new use cases, enabling optimization and automation capabilities that were simply unobtainable until now.
As an example, real-time data processing, made possible by ultra-low-latency wireless technologies, is a critical component of everything from mobile robotics to video-based safety monitoring and training simulators that use augmented and virtual reality (AR/VR). These are all use cases that legacy networks or Wi-Fi couldn’t support due to lag or inconsistent, unreliable communications speed.
New thinking for new networks
Use cases determine what’s needed of the network. And because the network is the foundation of Industry 4.0, providing the connectivity underlying every system, it needs to be the first thought when planning an Industry 4.0 upgrade, not the last.
“Companies that make network decisions as their first consideration are the most successful,” says Wang. “They’re working in a thoughtful way with the ecosystem, testing and iterating their way into transformation.”
For example, one important decision a company needs to make is whether to choose a fully on-premises network, a fully cloud-based network, or a hybrid network, which involves some cloud- based network elements along with some on-premises components. A hybrid network can deliver the advantages of the cloud while keeping critical or confidential data in-house for better protection.
The specific requirements of a company’s use cases need to be factored in because those will determine the specifications the network will need to follow. Often, an Industry 4.0 network requires a mix of private LTE, public networks and multi-access edge cloud. How those are integrated and utilized will affect speed, computing power, coverage and performance.
Security needs must also be considered early on. While perimeter security was the primary concern before Industry 4.0 — when network borders were well-defined — now everything is interconnected. With so many devices communicating with each other (rather than just with the network), lateral security needs to be factored into network design from the start.
Evolving skillsets for Industry 4.0
New kinds of network demands require new kinds of skills. But there aren’t many companies that have the full scope of Industry 4.0 and networking expertise in-house, so they’re often required to look to an external partner for support.
Similarly, networking partners many not be familiar with the ins and outs of each industry and sector — but a high level of expertise will be required to make the most of Industry 4.0’s flexibility, adaptability and ability to address specific use cases. Network engineers often need to be brought into the industrial environment to get familiar with industry demands so they develop the right solutions to address sector-specific problems.
“It used to be that traditional network models were applied to industrial settings, a solution that wasn’t really defined by the problem,” says Brillat. “Now, the needs of specific industries and environments are defining the network, creating tailor-made solutions.”
Change management is another skill that needs to be developed as companies adapt to the current industrial revolution. New technologies and networks require revisions to be made to established processes, which aren’t always warmly received. People at any level of a company can be resistant to change and get in the way of Industry 4.0-enabled evolution. Proper communication, positioning and training can all help mitigate these types of issues.
Making the most of Industry 4.0
The network is foundational to Industry 4.0, enabling countless devices to connect to the internet and each other. But what an Industry 4.0 network looks like depends on many different factors and a host of possible new use cases ranging from augmented reality applications to AI-driven automation.
There truly is no one-size-fits-all Industry 4.0 network architecture, but rather a wide range of possible networks with different strengths and specifications. Enterprises that embrace that flexibility and start thinking about what they need from the network early in their Industry 4.0 planning efforts will be well-positioned to take full advantage of the rapidly evolving potential of this new era of interconnected industry.
Want more insights?
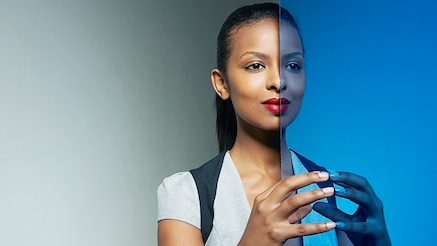
Article
Where can CSPs use digital twins
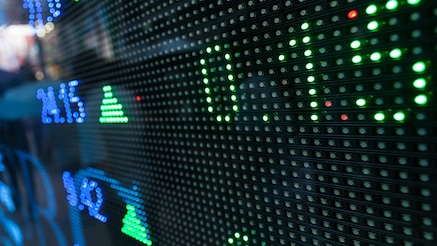
White paper