Why industrial devices are key enablers for Industry 4.0
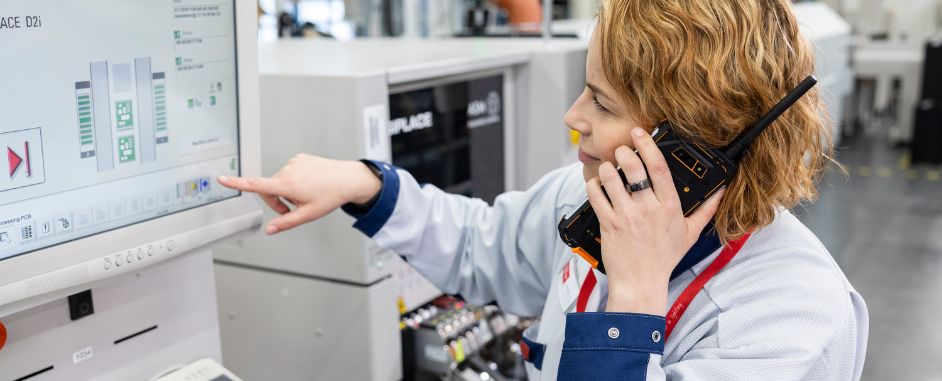
The rise of IT, mobile technologies and the internet has revolutionized productivity for many industries. Asset-intensive industries such as manufacturing, logistics, energy and transportation have benefited from these technologies but have not yet achieved the same productivity gains.
Industry 4.0 promises to accelerate development by enabling the digitalization of operational technology (OT) and related processes. To unlock the potential of Industry 4.0 technologies such as augmented and virtual reality (AR/VR), machine learning and digital twins, asset-intensive enterprises need to find effective ways to access, analyze and visualize their operational data.
Industrial devices play a central role in meeting this need by working with wireless networks, edge solutions and applications to enable reliable connectivity, efficient data handling and new capabilities that amplify the potential of workers and machines.
Four main enablers for Industry 4.0 success
Enterprises know that Industry 4.0 demands high-performance connectivity for Operational technology (OT) use cases. Many are deploying high capacity, low latency, reliable 4.9G/LTE or 5G private wireless networks to connect their people and machines.
Companies also know they need local computing capacity in an on-premises edge solution to ensure low latency and analytics capabilities for mission-critical applications, robots and autonomous vehicles.
Digital applications deployed on Edge are essential for Industry 4.0 because data needs to be processed on-premises, close to the industrial site to provide quick response and high performance. With advanced applications such as analytics, digital twins and indoor positioning, enterprises can support flexible, automated, data-driven operations.
Applications need devices that can connect and collect real-time data from workers, vehicles and machines. As the industrial environments, many times are harsh and the workers must use protective equipment, like helmets and gloves, it is not possible to take any consumer device for them to make phone and video calls, send messages and communicate their location. And only the newest assets have inbuilt capabilities to transfer data wirelessly.
A GlobalData and Nokia survey of early private wireless adopters highlights the growing role of devices in the Industry 4.0 technology mix. Sixty-three percent of respondents already use connected industrial devices. Another 27 percent are considering them for the near future. Figure 1 shows the most popular devices.
Figure 1: Market adoption of industrial devices
Enterprises need reliable, Industry 4.0-ready devices
Survey respondents are benefiting from these devices. For example, 95 percent reported an increase in worker collaboration, productivity and safety after they introduced private wireless and industrial digitalization solutions such as ruggedized 4G and 5G devices. These solutions provide business-critical communications and data feeds for teams and machines in challenging industrial environments.
Typically, industrial assets lack the capability to transfer data wirelessly, which is a key feature for vehicles and also increases the flexibility of fixed assets. Fieldrouters with industrial protocols can enable wireless data transfer, which brings Industry 4.0 to industries where assets have a long lifespan. Dongles are smaller and can be integrated in robots and AMRs to enable the connection to pervasive private wireless networks and reliable, continuous operations over large areas.
Audio and visual communication one-to-one and within groups is essential for work efficiency and safety. Ruggedized smartphones and handhelds, with customizable buttons that can be operated with gloves on and, connected to accessories ease the daily tasks. A big variety of earbuds, headsets, remote speaker microphones and wearable cameras serve the employees for push-to-talk and -video.
Enterprises want complete digitalization solutions, including devices
Early private wireless adopters say they want comprehensive digitalization solutions. For instance, 79 percent see the benefits of working with a vendor that can provide a comprehensive approach. Their reasons include fewer suppliers to manage (47 percent), increased return on investment (46 percent), lower total cost of ownership (39 percent) and faster deployment (33 percent).
Nokia is addressing the demand for end-to-end solutions with one platform for industrial digitalization. This platform simplifies Industry 4.0 transformation by combining industrial-grade private wireless, an industrial edge, an application ecosystem and a portfolio of high-quality industrial devices to connect workers, machines, sensors and other industrial assets.
Figure 2: One platform for industrial digitalization by Nokia
Industrial devices for smarter, safer connected operations
Nokia Industrial devices provide many options for enabling data transfer and human communication Our portfolio includes ruggedized equipment such as handhelds, smartphones, field routers, dongles, hotspots and 5G video cameras. It also includes wearable accessories such as headsets, earpieces, microphones and cameras.
We offer devices in different form factors to connect a big variety of industrial assets. We build them for heavy use in harsh environments such as mines, oil fields, ports, wind farms and chemical plants. Our devices are certified with high IP ratings. Some are ATEX/IECEx-certified for use in hazardous environments. They support the most common private wireless bands worldwide, including 4.9G/LTE, 5G, CBRS, MulteFire and unlicensed spectrum.
Our industrial devices are pre-configured and tested for use with our private wireless solutions. They can also be pre-installed with digital applications from our ecosystem-neutral application catalog. This fully integrated approach makes it easy and quick to connect teams, vehicles and equipment with guaranteed performance and ensure that they can always share information efficiently.
Nokia Industrial devices have built-in device management capabilities, including zero-touch onboarding and remote management. Enterprises can use a dashboard to view all devices, initiate maintenance actions or drill down to learn more about individual devices. The Nokia Network Digital Twin solution accelerates issue detection and resolution by collecting real-time data on how each device experiences the network.
Why choose Nokia Industrial devices?
- Reliably and securely connect mobile workers and industrial assets.
- Use real-time insights to make smarter decisions.
- Connect OT to enable compelling Industry 4.0 use cases.
- Boost productivity, efficiency, sustainability and safety.
Find out more
Read our brochure to learn more about how Nokia Industrial devices can help you get the most from Industry 4.0.