Insights and innovation
Pioneering a future where networks meet cloud
Technology is rapidly evolving. Keep up to date with the innovations we are developing and our perspectives on the trends that are supercharging networks.
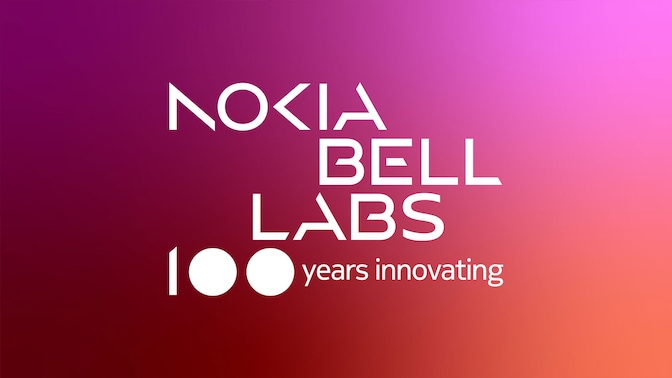
Nokia Bell Labs
Nokia Bell Labs
Explore Bell Labs' century of innovation, from pioneering the transistor, shaping communications to driving future technologies with real-world impact.
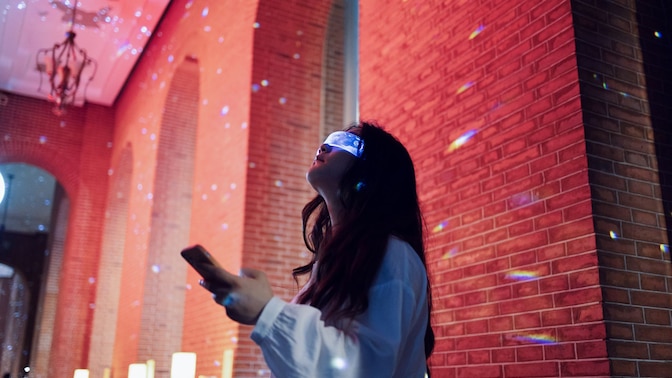
Thought Leadership
Amplifying insights from industry experts.
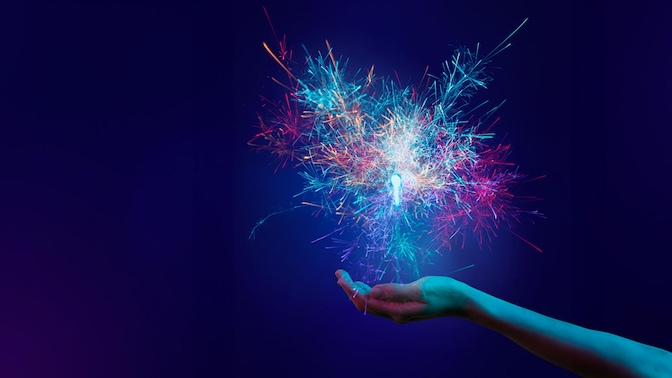
Innovate with Nokia
Building a global ecosystem of innovation.
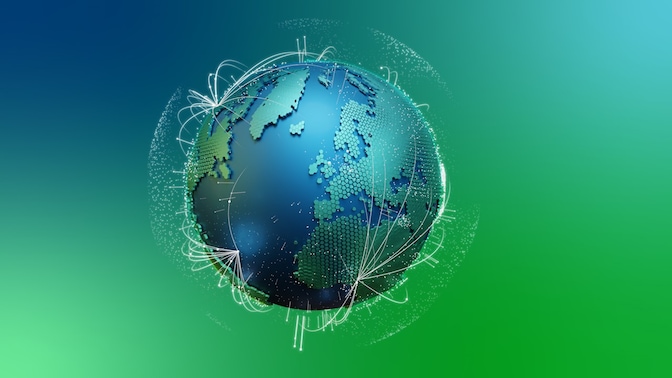
Standardization
We are spearheading global technology standards for a safer, modern world.
Get to know the future as we see it evolving

Strategy
Technology strategy
Shaping the hyper-digital world.
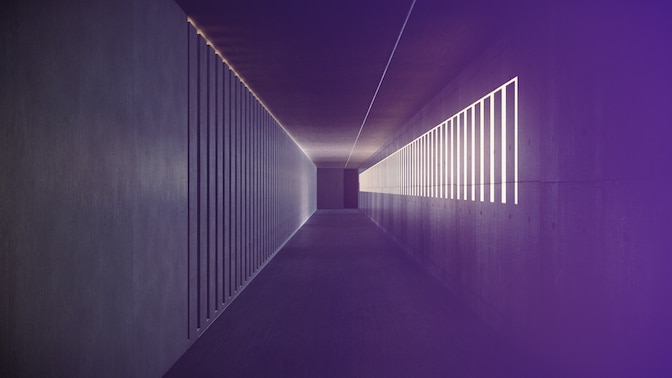
Vision
Technology vision
Digital acceleration toward a new quantum era.